Plastic extrusion for tubing, sections, and custom shapes
Plastic extrusion for tubing, sections, and custom shapes
Blog Article
Understanding the Essentials and Applications of Plastic Extrusion in Modern Production
In the world of modern production, the method of plastic extrusion plays a critical function - plastic extrusion. This intricate procedure, including the melting and shaping of plastic through specialized dies, is leveraged across different sectors for the production of varied products. From vehicle components to durable goods packaging, the applications are large, and the potential for sustainability is similarly remarkable. Unwinding the basics of this process discloses truth adaptability and capacity of plastic extrusion.
The Principles of Plastic Extrusion Process
While it might appear facility, the principles of the plastic extrusion process are based on reasonably straightforward concepts. It is a production procedure wherein plastic is thawed and after that shaped into a continual account with a die. The raw plastic material, frequently in the type of pellets, is fed right into an extruder. Inside the extruder, the plastic goes through heat and stress, causing it to thaw. The molten plastic is after that compelled through a designed opening, referred to as a die, to form a long, constant item. The extruded product is cooled and after that reduced to the preferred size. The plastic extrusion procedure is thoroughly made use of in various sectors due to its cost-effectiveness, versatility, and performance.
Various Types of Plastic Extrusion Strategies
Building upon the standard understanding of the plastic extrusion procedure, it is essential to discover the different strategies associated with this manufacturing method. The 2 primary techniques are profile extrusion and sheet extrusion. In profile extrusion, plastic is melted and created into a constant profile, commonly utilized to create pipelines, poles, rails, and window frameworks. On the other hand, sheet extrusion creates huge, flat sheets of plastic, which are usually additional refined into items such as food try this product packaging, shower curtains, and auto components. Each strategy calls for specialized machinery and precise control over temperature level and pressure to ensure the plastic keeps its form throughout cooling. Recognizing these strategies is crucial to utilizing plastic extrusion properly in contemporary manufacturing.

The Role of Plastic Extrusion in the Automotive Market
A frustrating bulk of components in modern lorries are products of the plastic extrusion process. Plastic extrusion is primarily made use of in the manufacturing of various car parts such as bumpers, grills, door panels, and dashboard trim. Thus, plastic extrusion plays a critical function in vehicle production.
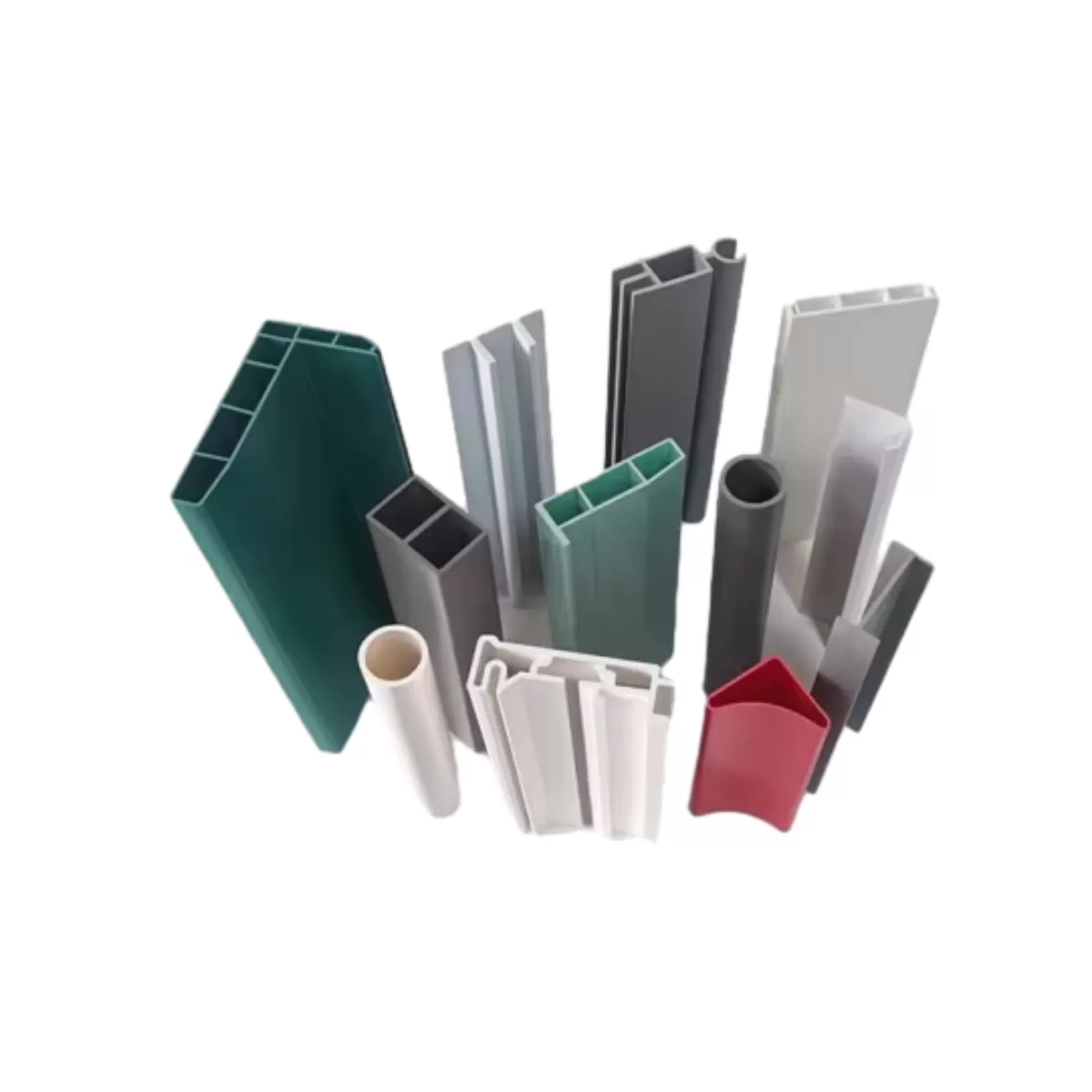
Applications of Plastic Extrusion in Consumer Goods Production
Beyond its substantial influence on the vehicle plastic extrusion sector, plastic extrusion proves just as reliable in the world of durable goods producing. This procedure is critical in producing a large range of products, from food product packaging to home appliances, toys, and even clinical devices. The flexibility of plastic extrusion allows manufacturers to create and generate complicated sizes and shapes with high accuracy and effectiveness. Due to the recyclability of many plastics, extruded elements can be reprocessed, lowering waste and expense (plastic extrusion). The adaptability, my site flexibility, and cost-effectiveness of plastic extrusion make it a preferred selection for numerous durable goods producers, adding substantially to the industry's growth and technology. The ecological effects of this extensive usage require mindful consideration, a subject to be discussed further in the subsequent section.
Ecological Influence and Sustainability in Plastic Extrusion
The pervasive use of plastic extrusion in producing invites examination of its eco-friendly ramifications. Reliable equipment minimizes power usage, while waste administration systems reuse scrap plastic, reducing raw material demands. Regardless of these enhancements, even more innovation is needed to alleviate the environmental footprint of plastic extrusion.
Conclusion
In verdict, plastic extrusion plays an important function in modern manufacturing, specifically in the automobile and consumer products markets. Understanding the fundamentals of this procedure is key to enhancing its benefits and applications.

The plastic extrusion procedure is extensively made use of in different markets due to its flexibility, cost-effectiveness, and efficiency.
Structure upon the standard understanding of the plastic extrusion procedure, it is essential to discover the various strategies involved in this manufacturing technique. plastic extrusion. In comparison, sheet extrusion produces large, flat sheets of plastic, which are commonly additional refined right into items such as food packaging, shower drapes, and auto components.A frustrating majority of parts in contemporary cars are products of the plastic extrusion procedure
Report this page