Plastic extrusion for detailed profiles and custom designs
Plastic extrusion for detailed profiles and custom designs
Blog Article
Comprehending the Essentials and Applications of Plastic Extrusion in Modern Production
In the world of modern manufacturing, the technique of plastic extrusion plays a critical duty - plastic extrusion. This elaborate procedure, entailing the melting and shaping of plastic through specialized passes away, is leveraged throughout numerous markets for the development of varied items. From vehicle parts to durable goods packaging, the applications are vast, and the possibility for sustainability is similarly excellent. Deciphering the basics of this process discloses truth adaptability and possibility of plastic extrusion.
The Principles of Plastic Extrusion Refine
While it might appear complex, the fundamentals of the plastic extrusion process are based upon fairly simple concepts. It is a manufacturing process wherein plastic is thawed and after that shaped into a continual account through a die. The raw plastic product, typically in the form of pellets, is fed into an extruder. Inside the extruder, the plastic goes through warm and pressure, triggering it to melt. The molten plastic is after that compelled with a shaped opening, called a die, to form a long, constant product. The extruded product is cooled and after that cut to the wanted size. The plastic extrusion process is extensively used in various markets due to its convenience, cost-effectiveness, and effectiveness.
Various Kinds Of Plastic Extrusion Techniques
Structure upon the basic understanding of the plastic extrusion procedure, it is necessary to check out the different techniques associated with this manufacturing approach. The two main techniques are profile extrusion and sheet extrusion. In account extrusion, plastic is melted and created right into a continual account, frequently utilized to develop pipelines, rods, rails, and home window structures. On the other hand, sheet extrusion produces huge, flat sheets of plastic, which are generally further processed right into products such as food packaging, shower curtains, and cars and truck components. Each method requires specialized equipment and specific control over temperature and stress to make certain the plastic keeps its form during cooling. Understanding these techniques is key look here to using plastic extrusion efficiently in modern-day manufacturing.
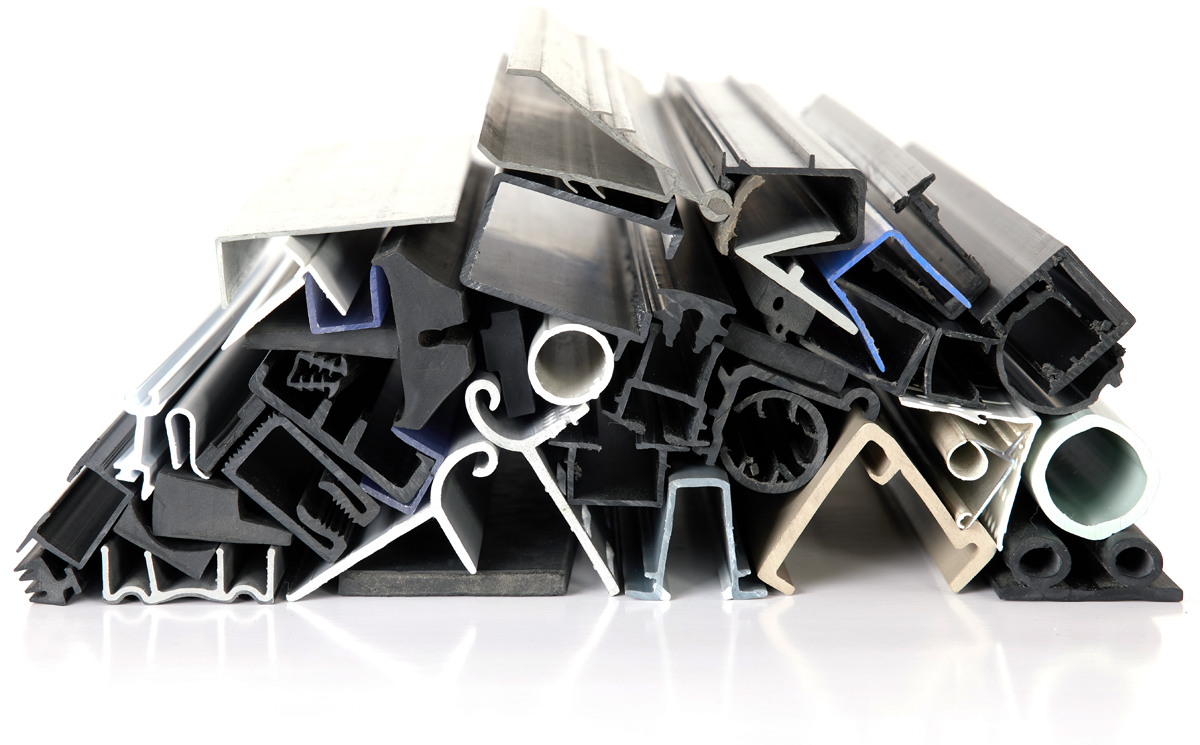
The Duty of Plastic Extrusion in the Automotive Industry
A frustrating bulk of components in contemporary automobiles are items of the plastic extrusion procedure. This process has revolutionized the vehicle market, changing it into a more effective, cost-effective, and flexible production field. Plastic extrusion is mostly used in the production of various automobile elements such as bumpers, grills, door panels, and dashboard trim. The process provides an uniform, regular output, enabling suppliers to create high-volume components with excellent precision and very little waste. The lightness of the extruded plastic parts adds to the overall decrease in lorry weight, boosting gas efficiency. The longevity and resistance of these components to warmth, cold, and effect improve the longevity of autos. Hence, plastic extrusion plays an essential role in vehicle production.
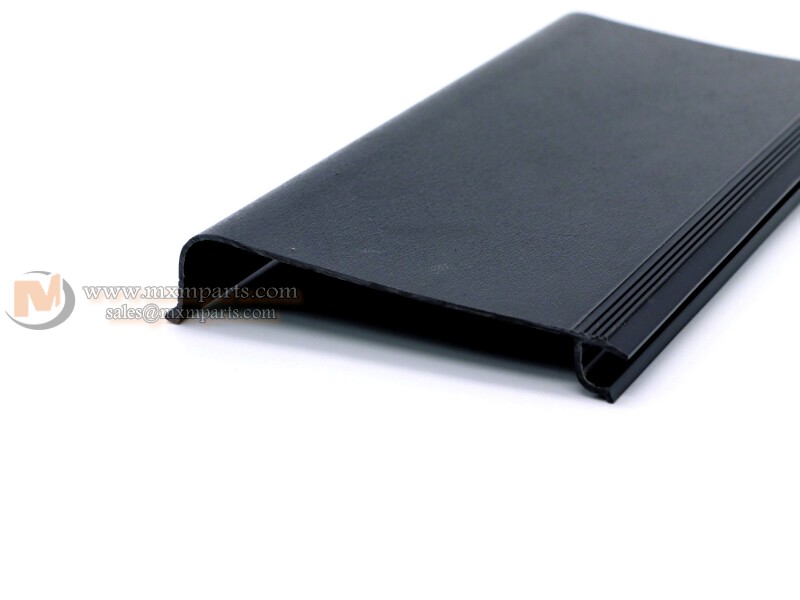
Applications of Plastic Extrusion in Durable Goods Production
Past its significant effect on the auto market, plastic extrusion verifies similarly effective in the realm of consumer goods manufacturing. The convenience of plastic extrusion enables manufacturers to develop and produce intricate shapes and dimensions with high accuracy and efficiency. The versatility, flexibility, and cost-effectiveness of plastic extrusion make it a recommended selection for many customer products makers, adding substantially to the industry's growth and technology.
Ecological Influence and Sustainability in Plastic Extrusion
The pervasive usage of plastic extrusion in producing welcomes scrutiny of its ecological implications. As a process that often makes use of non-biodegradable materials, the ecological influence Find Out More can be significant. Power click here for more info intake, waste production, and carbon exhausts are all concerns. Sector advancements are boosting sustainability. Effective machinery lowers energy usage, while waste management systems reuse scrap plastic, decreasing resources needs. Furthermore, the advancement of naturally degradable plastics provides an extra eco-friendly option. Despite these enhancements, further innovation is needed to mitigate the environmental footprint of plastic extrusion. As culture leans towards sustainability, manufacturers should adjust to remain sensible, stressing the relevance of continuous research and improvement in this area.
Verdict
In final thought, plastic extrusion plays an essential role in modern-day manufacturing, especially in the automotive and customer goods fields. Recognizing the essentials of this procedure is key to optimizing its benefits and applications.
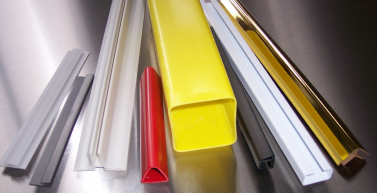
The plastic extrusion process is extensively utilized in numerous sectors due to its cost-effectiveness, efficiency, and flexibility.
Structure upon the standard understanding of the plastic extrusion process, it is essential to explore the different strategies entailed in this production approach. plastic extrusion. In contrast, sheet extrusion creates big, level sheets of plastic, which are normally additional refined right into items such as food product packaging, shower drapes, and automobile components.An overwhelming bulk of parts in modern-day automobiles are items of the plastic extrusion process
Report this page